Cold blade guillotines for plastic profiles

TG.G-CB
Baruffaldi’s patented cold blade cutting guillotines are designed for profiles of small dimensions and reduced thickness, and are available in in-line and off-line versions, depending on the type of application required.
These units are designed to efficiently cut profiles extruded also in more than one strand, as well as for multiple cuts. They stand out for their horizontal cutting system, which prevents any profile deformation and guarantees a high standard in the quality of the cut.
Our guillotines are available in the different versions: they can be pneumatic (TG.G-PP-CB), pneumatic/ servo-aided (TG.G-PD-CB or TG.G-DP-CB), or completely servo-driven, for an extremely precise cut, with up to ± 0,5 mm tolerance, at a high speed.
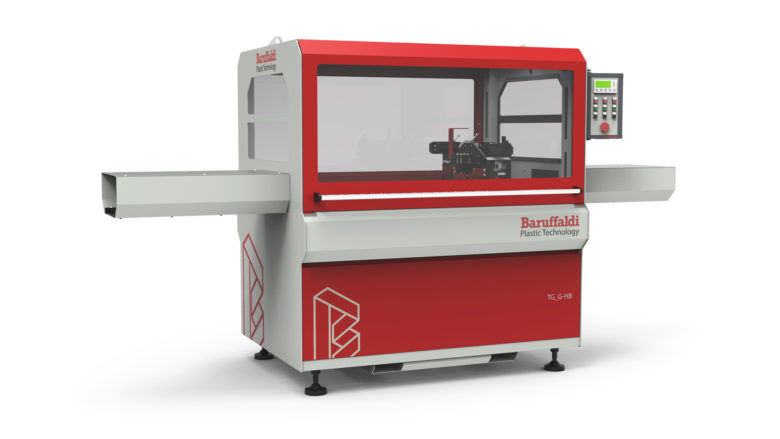
Our internal technical office can customize the various guillotine cutting units based on the specific production needs and customers’ requirements.
Thanks to their modularity and compact size of our guillotines it is possible to fit the stand-alone machine in an existing extrusion line, or fix the mere cutting assembly onto the saw machine frame.
Advantages
- No noise during the cut
- Clean, precise cut with no dust of swarf/burrs
- Highly versatile for different applications
- No material waste
- Leading brand components
- Customised software according to customer needs
- Process reliability and energy saving
- Reduction of production costs, thanks to high productivity and low maintenance costs
- Easy use and quick cut set (die block and blade) changeover
Technical features
- Solidità, robustezza e versatilità
- Adatte al taglio di profili estrusi in materiali plastici diversi (es. PVC, PC, PC/ABS, PP, PE )
- Guida della lama in acciaio temprato e rettificato
- Ottimizzazione delle matrici di taglio per più profili